In the era of Industry 4.0, technological advancements are profoundly transforming the landscape of manufacturing and supply chain management. A pivotal innovation of the fourth industrial revolution is the integration of robotics across various sectors to enhance efficiency and productivity. Robots offer several advantages, some of which include:
- Increased efficiency
- Precision
- The ability to perform repetitive tasks without fatigue
- Enhanced safety by taking over hazardous duties from human workers
Robots have been steadily increasing its presence in manufacturing, healthcare, and logistics, etc. In manufacturing, robots are used in assembly lines for welding, painting, and packaging which significantly increases production speed and reduces errors. In healthcare, robots assist in surgeries, patient care, and logistics within hospitals, improving patient outcomes and operational efficiency. In logistics, autonomous robots are employed for sorting, packing, and transporting goods within warehouses, thus optimizing the supply chain process.
Implementation of robotics in various sectors
Numerous robotics initiatives have found support and success in Singapore. For instance, the National Robotics Programme (NRP) is investing S$60 million in the ready adoption of robotics in various industries in Singapore. Meanwhile, Changi General Hospital (CGH) has deployed three innovative robots to enhance patient care and streamline operations within the Emergency Department (ED). These robots include one that handles medication delivery, one that assists patients with wayfinding, and the last one that delivers blankets to patients. These investments and the adoption of robots underscores Singapore’s commitment to leveraging advanced technologies to enhance productivity and economic growth.
As technology advances, industries are increasingly adopting more advanced and productive robotic systems due to the clear benefits they offer. However, the successful integration of robotics into established workplaces involves more than just deploying machines; it necessitates thoughtful coordination and adaptation.
In controlled environments, such as warehouses or manufacturing facilities, the deployment of robots seems straightforward. Algorithms govern their actions and they follow predefined rules to optimise processes. Yet, the reality is far more complex. Rather than replacing human workers entirely, robots often collaborate with them. This collaboration requires seamless interaction, shared spaces, and segregation of tasks which adds to the complexity of the system.
One clear case where this complexity is very prominent is in the use of robotics in warehouse automation. Automated systems within warehouses, such as robotic pickers and Automated Storage and Retrieval Systems (AS/RS), significantly reduce the time needed to process orders and minimize human error. This automation ensures that warehouses can handle high volumes of orders with precision and speed, which is crucial for meeting customer expectations in the fast-paced e-commerce environment. Major logistics service providers, including Alibaba, JD Logistics, and Amazon, have more than 100,000 robots in their fulfillment centers. According to ABI Research, the number of commercial robots will reach four million by 2025, a twentyfold increase from 2018.
Among the myriad processes within a warehouse, order picking stands out as particularly demanding in terms of time and resources. Order picking involves selecting items from the inventory to fulfil customer orders. Therefore, its efficiency is critical to overall warehouse productivity. This process is inherently time consuming and error prone in addition to causing congestion in the facility and hence has been a major focus of automation for the industry, with the introduction of AS/RS, conveyer systems, mobile robots, etc.
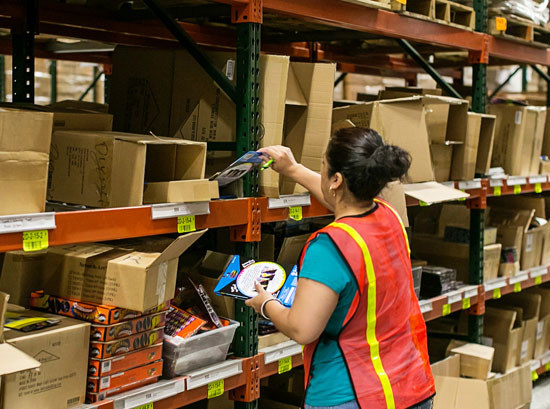
Order Picking in a Mobile-Rack Part-to-Picker System
As a part of warehouse automation, lots of companies adopt a “part-to-picker” system. This human-machine system incorporates a fleet of robots, mobile racks, workstations, and advanced control software, offering a novel approach to enhance the efficiency of the order picking process. In a warehouse employing this system, robots are programmed to transport racks to designated stations, where human operators retrieve items from the racks and deposit them into bins. By entrusting the labor-intensive task of carrying to the robots, the system is anticipated to significantly decrease the walking distance covered by human operators, improving order picking productivity.
Despite offering an increase in efficiency, the emergence of warehouse automation brings new challenges. One of the major challenges involves navigating the interaction between human pickers and robot movers. It is crucial to acknowledge the dynamic nature of human pickers’ working states and their susceptibility to fatigue. Often, the mismatch between the performance of robots and humans leads to the risk of being overworked. So, overlooking human working states when establishing the schedule for the movement of mobile racks by robots can quickly turn counterproductive.
In “Robot Scheduling for Mobile-Rack Warehouses: Human–Robot Coordinated Order Picking Systems,” the Wang et al. address the optimisation of rack assignments for multiple pickers with diverse working states, aiming to enhance overall picking productivity. The authors develop an effective scheduling strategy for all assigned racks, with the primary objective of minimising the total expected picking time.
The main challenge lies in anticipating the worker’s fatigue and scheduling activities to not overburden an individual for prolonged periods of time. The authors employ a data-driven approach to determine the state transition probabilities (for instance, workload encountered in previous task or staggered break times will result in the individuals with different fatigue levels) of each picker. At the same time, they solve the job assignment and sequencing problem in order to minimize the backlog of racks awaiting processing.
The problem was modelled as a stochastic Dynamic program and an Approximate Dynamic Program based Branch-and-price algorithm was developed to solve the model. The overall impact of the study results in reducing the queues at each station while the worker is engaged in the picking process. This study shows that considering human factors while introducing automation, in particular the order picking proces has these major implications:
- Robot scheduling has direct effects on the working states of human pickers, which would further influence the performance of an order picking system,
- Pickers’ degrees of fluctuation of working states may vary significantly. However, this variation does not result in a large variation among their picking times if scheduling is effective.
- Understanding fluctuations of human working states and responding to them proactively can improve the performance of human–robot coordinated systems.
Overall, the surge in e-commerce has redefined retail, emphasising the pivotal role of warehouses in the supply chain. Efficient inventory management, particularly in the context of order picking, becomes paramount for overall warehouse productivity. The study demonstrates a noteworthy 10% reduction in picking time when a human-robot coordination is considering in planning the tasks, thereby underscoring the potential for substantial cost savings and efficiency improvements.